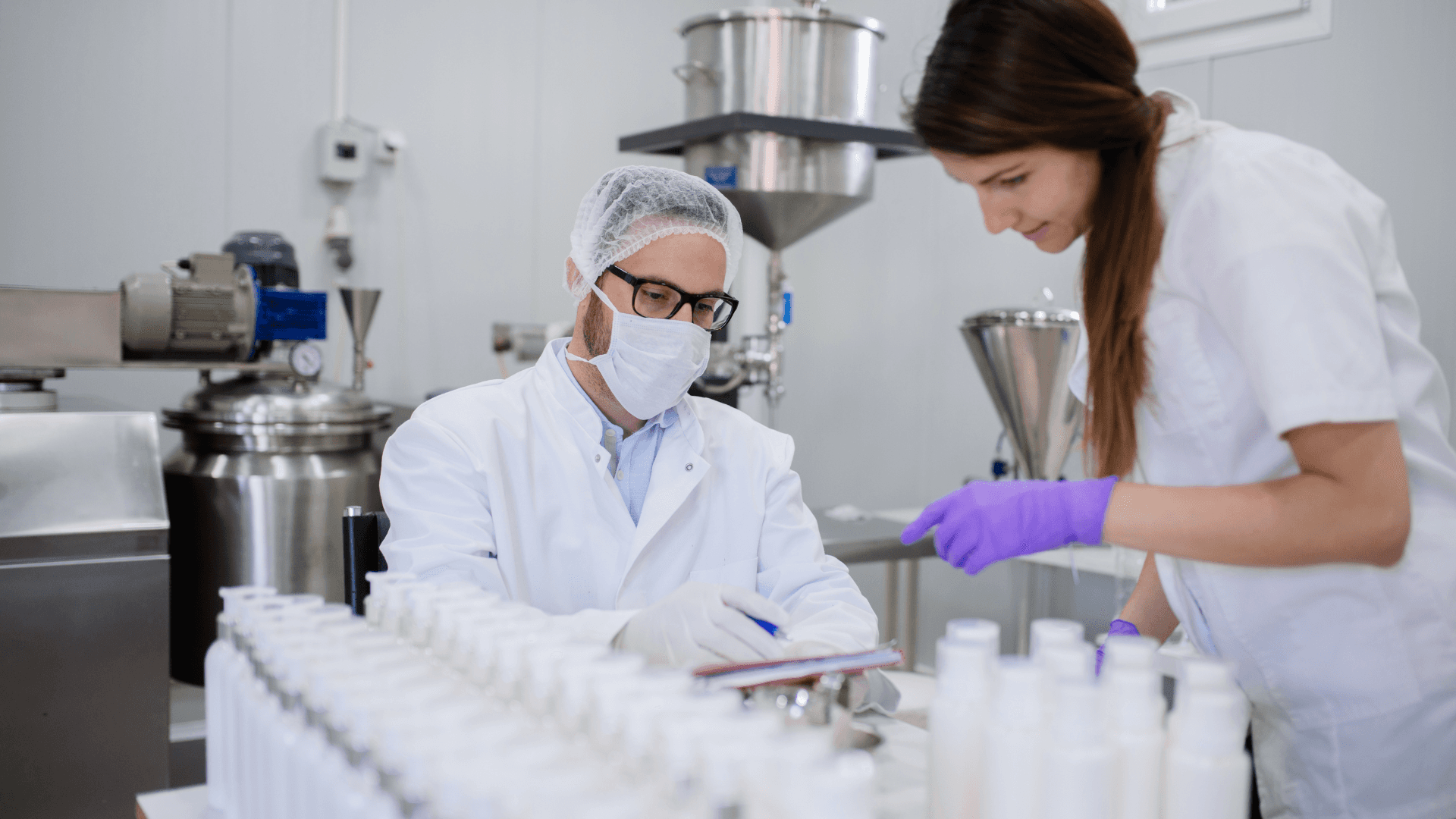
Cosmetic production: visual quality defects to avoid
Published on
Sep 4, 2024
by
Scortex team
In the field of cosmetic production, product quality is paramount to meet customer requirements and comply with strict industry standards. Visual quality defects are among the most common and can seriously damage a brand’s reputation. Here are the main visual defects to avoid in cosmetic production and the best practices to prevent them.
1. Air bubbles and surface irregularities
Air bubbles in creams, gels or lotions are common visual defects. They can be caused by poor mixing technique or faulty equipment. Proper mixing methods and regular equipment checks are essential to ensure quality production. Regular visual inspections by production line operators can help detect these defects early in the process.
2. Color change
Color variations in cosmetic products can indicate formulation or stability issues. These changes can be caused by unexpected chemical reactions or excessive exposure to light. Using quality raw materials and performing rigorous stability testing helps prevent these issues. Automated inspection with machine vision cameras can also detect subtle color variations.
3. Foreign particles
The presence of foreign particles in cosmetic products is not only a visual defect, but also a health risk to consumers. To avoid this problem, it is crucial to ensure a clean production environment and follow strict cleaning protocols. Automated inspections can complement manual inspections by detecting tiny particles that may escape the human eye.
4. Labeling defects
Poorly adhered, torn, or poorly printed labels can give a poor impression of quality to customers. Inspectors must ensure that labels are correctly applied and legible. Using automated inspection systems to verify labeling can ensure consistent compliance with standards.
5. Packaging issues
Defects such as faulty caps, leaks, or damaged containers can negatively impact the user experience. To prevent these issues, manufacturers must conduct rigorous checks of packaging materials and tightening tests to ensure product integrity. Automated inspections can be used to verify packaging quality at every stage of production.
6. Inconsistent textures
Variations in texture, such as lumps or uneven consistency, can affect product application and efficacy. Regular inspections and rigorous quality checks are essential to ensure consistent texture. AI can play a key role by analyzing textures and detecting inconsistencies early.
7. Uneven finishes
Product surfaces must be smooth and free of visible defects such as scratches or dents. Machine vision techniques can be used to detect these finishing defects. Operators must also be trained to identify and correct these issues before products leave the factory.
To achieve a high level of quality control in cosmetics production, it is essential to combine manual and automated inspections. This allows visual defects to be detected and corrected before products reach customers. By integrating machine vision and AI technologies, manufacturers can improve the quality of their products and reduce customer complaints. For a quick and easy-to-deploy quality inspection solution, Scortex Spark is the ideal tool, offering real-time data analytics and implementation without costly expertise.
Here are other articles that may interest you:
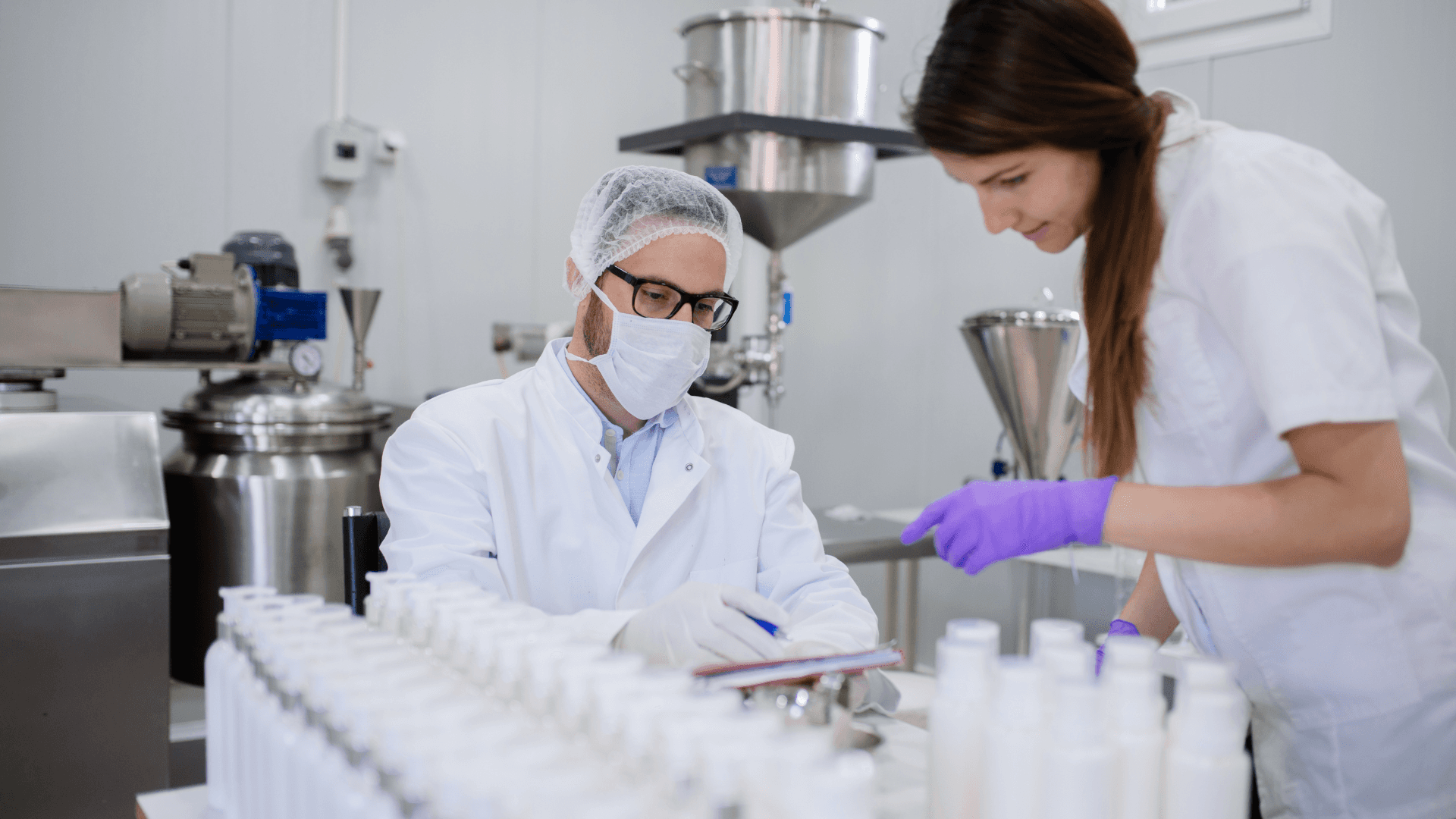
Cosmetic production: visual quality defects to avoid
Published on
Sep 4, 2024
by
Scortex team
In the field of cosmetic production, product quality is paramount to meet customer requirements and comply with strict industry standards. Visual quality defects are among the most common and can seriously damage a brand’s reputation. Here are the main visual defects to avoid in cosmetic production and the best practices to prevent them.
1. Air bubbles and surface irregularities
Air bubbles in creams, gels or lotions are common visual defects. They can be caused by poor mixing technique or faulty equipment. Proper mixing methods and regular equipment checks are essential to ensure quality production. Regular visual inspections by production line operators can help detect these defects early in the process.
2. Color change
Color variations in cosmetic products can indicate formulation or stability issues. These changes can be caused by unexpected chemical reactions or excessive exposure to light. Using quality raw materials and performing rigorous stability testing helps prevent these issues. Automated inspection with machine vision cameras can also detect subtle color variations.
3. Foreign particles
The presence of foreign particles in cosmetic products is not only a visual defect, but also a health risk to consumers. To avoid this problem, it is crucial to ensure a clean production environment and follow strict cleaning protocols. Automated inspections can complement manual inspections by detecting tiny particles that may escape the human eye.
4. Labeling defects
Poorly adhered, torn, or poorly printed labels can give a poor impression of quality to customers. Inspectors must ensure that labels are correctly applied and legible. Using automated inspection systems to verify labeling can ensure consistent compliance with standards.
5. Packaging issues
Defects such as faulty caps, leaks, or damaged containers can negatively impact the user experience. To prevent these issues, manufacturers must conduct rigorous checks of packaging materials and tightening tests to ensure product integrity. Automated inspections can be used to verify packaging quality at every stage of production.
6. Inconsistent textures
Variations in texture, such as lumps or uneven consistency, can affect product application and efficacy. Regular inspections and rigorous quality checks are essential to ensure consistent texture. AI can play a key role by analyzing textures and detecting inconsistencies early.
7. Uneven finishes
Product surfaces must be smooth and free of visible defects such as scratches or dents. Machine vision techniques can be used to detect these finishing defects. Operators must also be trained to identify and correct these issues before products leave the factory.
To achieve a high level of quality control in cosmetics production, it is essential to combine manual and automated inspections. This allows visual defects to be detected and corrected before products reach customers. By integrating machine vision and AI technologies, manufacturers can improve the quality of their products and reduce customer complaints. For a quick and easy-to-deploy quality inspection solution, Scortex Spark is the ideal tool, offering real-time data analytics and implementation without costly expertise.
Here are other articles that may interest you:

Let's discuss your quality today.

Scortex team is happy to answer your questions.
Let's discuss your quality today.

Scortex team is happy to answer your questions.
Join our newsletter
Join our newsletter