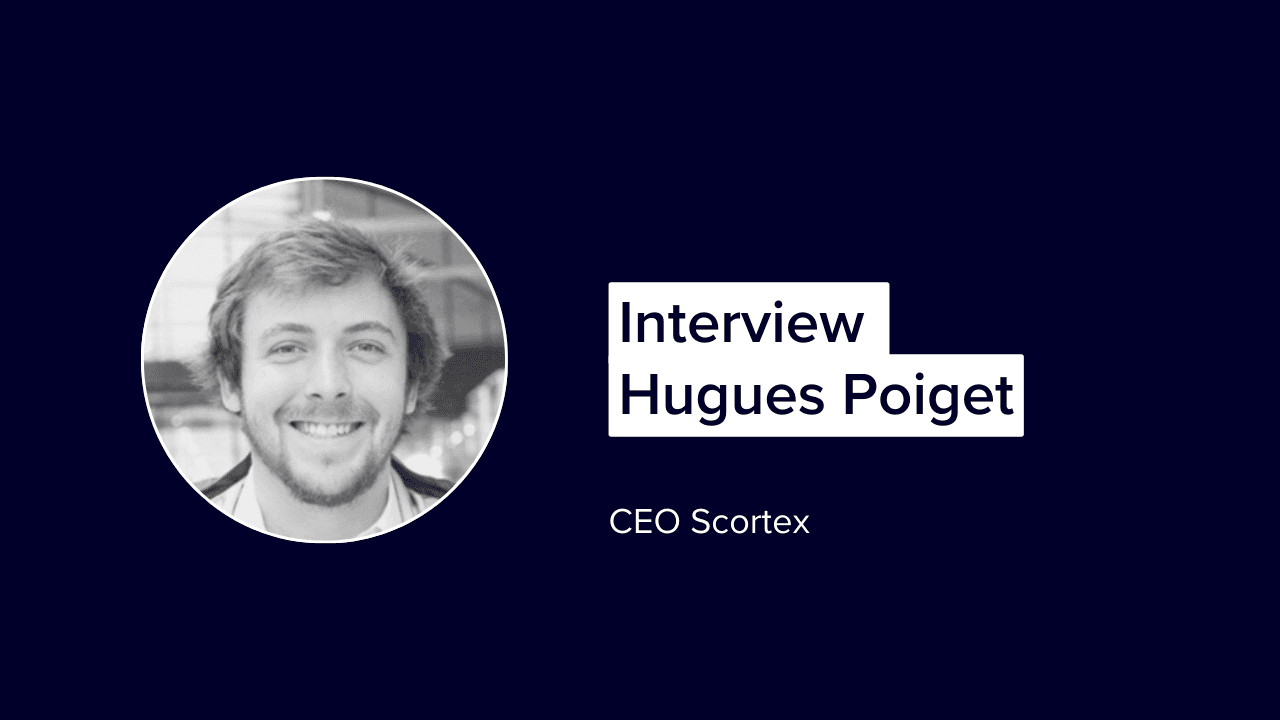
Interview with Hugues Poiget, Scortex CEO
Published on
Nov 21, 2024
by
Scortex Team
What a pleasure it is to hear one of our clients tell us they reduced their scrap rate from 7% to 2% in just one month!
Interview with Hugues POIGET, CEO of Scortex, a French company founded in 2016 and now part of the Trigo Group, a leader in operational quality. Scortex is committed to automating, transforming, and streamlining visual inspections in industrial production with its AI-powered quality control solutions.
Could you introduce Scortex and explain its mission in the industry?
Hugues Poiget: At Scortex, we help manufacturers reduce the cost of inspecting 100% of their production by developing Artificial Intelligences and designing vision systems that allow them to check the appearance of the parts they produce. Our mission goes beyond sorting parts: our vision is to generate, through Spark—our quality control automation system—the data needed to optimize production. In the future, we can imagine production machine parameters being adjusted in real-time based on the quality measured by our systems at the end of the line.
What technology powers Spark, and why is it an asset for manufacturers?
Hugues Poiget: At Scortex, we train machines to sort parts and categorize defects. To sort parts, the system must look at the part, possibly rotate it, inspect all its sides, and then decide whether to reject it. For this, we have chosen cutting-edge technologies, ranging from Artificial Intelligence to ensure detection performance is as good as human capabilities, to PLC automation (robust industrial digital computers for controlling manufacturing processes) for real-time decision-making, such as triggering a robotic arm to eject defective parts. Of course, we’re not magicians—defects must be visible. To achieve this, we drew inspiration from how human operators inspect parts and developed lighting and imaging techniques that enable us to inspect even reflective parts, which are very common in industries such as cosmetics, medical devices, automotive, and others. Because we use AI, the solutions we deploy are like a new recruit that needs to be trained on the production line. We start by teaching the machine what compliant parts look like. The AI can then detect deviations from acceptable variability. A human confirms what is and isn’t acceptable during this phase before the AI takes the leap into full operation. Unlike humans, the system doesn’t reject parts unnecessarily due to forklift lights entering the inspection area or a drop of oil remaining on a machined part. It’s precisely to address these very real challenges that we’ve set up a dedicated team, which our clients confirm, adds enormous value.
Which industries benefit the most from Spark?
Hugues Poiget: We’ve always aimed for our systems to be relevant across a wide range of industries. Our systems inspect everything from automotive gearbox forks to lipstick. Although we started in the automotive sector, we are now present in cosmetics, aerospace, packaging, medical devices, luxury goods, forging, and electronics, to name a few. To date, tens of millions of parts produced by small and medium-sized enterprises as well as major international groups have been inspected by our systems and are now in the hands of end users.
How does Scortex integrate with the Trigo Group, and how does this strengthen its positioning?
Hugues Poiget: At Scortex, we’ve always been very hands-on, and thanks to Trigo, we now have access to over 300 factories in more than 25 countries. This was an incredible opportunity we were eager to seize to move forward together. What unites us is a shared comprehensive approach to quality. The costs of quality are multifaceted: scrap, training, penalties, recalls, and more. Trigo now allows us to operate beyond Europe—in the United States, Canada, Brazil, India, and more recently South Korea—with an unmatched level of responsiveness.
What are the key trends in industrial quality control that Scortex anticipates?
Hugues Poiget: We aim to support quality controllers in all their key tasks: sparing them from eight-hour shifts of inspecting parts for anomalies, speeding up their ability to distinguish between acceptable and unacceptable anomalies, and providing quality data so they can quickly adjust sorting criteria based on production volumes. One major trend we anticipate is that AI-based tools will rapidly become commodities. The recent example of ChatGPT is a case in point. AI is entering everyday life and is already making its way into factories. This will, among other things, give manufacturers a competitive edge. Another trend is the need to reduce the environmental impact of industry. At Scortex, we understand the importance of reconciling production requirements with quality obligations. This is essential for maintaining a certain standard of living accessible to the majority. Tools like ours, by improving production line efficiency, help minimize the use of energy and raw materials.
Why do manufacturers choose Scortex for their automated quality control needs?
Hugues Poiget: At Scortex, we’re not afraid to roll up our sleeves. This is necessary to move from proof of concept to a system fully integrated into a production line. Our clients come to us looking for a powerful yet simple solution to the complex problem of visual inspection. Our Spark product combines a tool that can be used by a quality operator directly on the production line with a control tower, called the Quality Center, where quality data from the factory is aggregated to optimize production. Scortex provides everything—from hardware to software to algorithms. And because quality is constantly evolving, our teams are ready to support manufacturers at every stage of the project.
What a pleasure it is to hear one of our clients tell us they reduced their scrap rate from 7% to 2% in just one month!
Here are some other articles that might interest you:
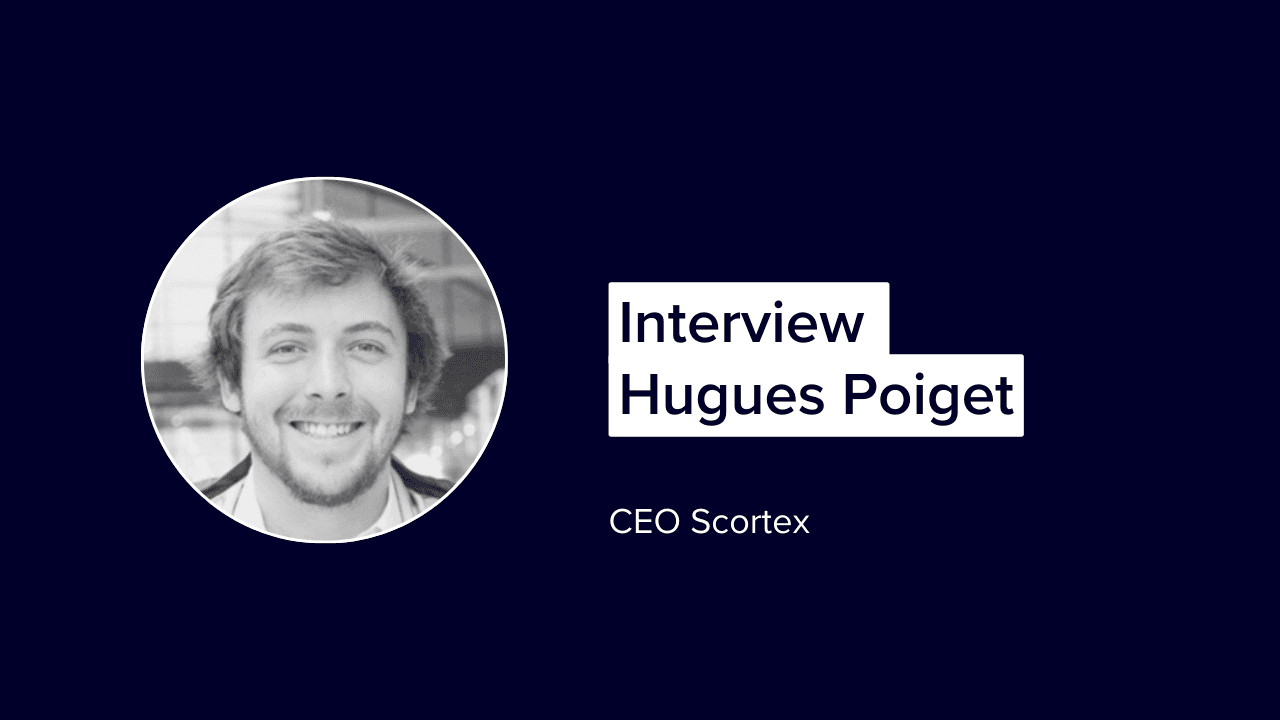
Interview with Hugues Poiget, Scortex CEO
Published on
Nov 21, 2024
by
Scortex Team
What a pleasure it is to hear one of our clients tell us they reduced their scrap rate from 7% to 2% in just one month!
Interview with Hugues POIGET, CEO of Scortex, a French company founded in 2016 and now part of the Trigo Group, a leader in operational quality. Scortex is committed to automating, transforming, and streamlining visual inspections in industrial production with its AI-powered quality control solutions.
Could you introduce Scortex and explain its mission in the industry?
Hugues Poiget: At Scortex, we help manufacturers reduce the cost of inspecting 100% of their production by developing Artificial Intelligences and designing vision systems that allow them to check the appearance of the parts they produce. Our mission goes beyond sorting parts: our vision is to generate, through Spark—our quality control automation system—the data needed to optimize production. In the future, we can imagine production machine parameters being adjusted in real-time based on the quality measured by our systems at the end of the line.
What technology powers Spark, and why is it an asset for manufacturers?
Hugues Poiget: At Scortex, we train machines to sort parts and categorize defects. To sort parts, the system must look at the part, possibly rotate it, inspect all its sides, and then decide whether to reject it. For this, we have chosen cutting-edge technologies, ranging from Artificial Intelligence to ensure detection performance is as good as human capabilities, to PLC automation (robust industrial digital computers for controlling manufacturing processes) for real-time decision-making, such as triggering a robotic arm to eject defective parts. Of course, we’re not magicians—defects must be visible. To achieve this, we drew inspiration from how human operators inspect parts and developed lighting and imaging techniques that enable us to inspect even reflective parts, which are very common in industries such as cosmetics, medical devices, automotive, and others. Because we use AI, the solutions we deploy are like a new recruit that needs to be trained on the production line. We start by teaching the machine what compliant parts look like. The AI can then detect deviations from acceptable variability. A human confirms what is and isn’t acceptable during this phase before the AI takes the leap into full operation. Unlike humans, the system doesn’t reject parts unnecessarily due to forklift lights entering the inspection area or a drop of oil remaining on a machined part. It’s precisely to address these very real challenges that we’ve set up a dedicated team, which our clients confirm, adds enormous value.
Which industries benefit the most from Spark?
Hugues Poiget: We’ve always aimed for our systems to be relevant across a wide range of industries. Our systems inspect everything from automotive gearbox forks to lipstick. Although we started in the automotive sector, we are now present in cosmetics, aerospace, packaging, medical devices, luxury goods, forging, and electronics, to name a few. To date, tens of millions of parts produced by small and medium-sized enterprises as well as major international groups have been inspected by our systems and are now in the hands of end users.
How does Scortex integrate with the Trigo Group, and how does this strengthen its positioning?
Hugues Poiget: At Scortex, we’ve always been very hands-on, and thanks to Trigo, we now have access to over 300 factories in more than 25 countries. This was an incredible opportunity we were eager to seize to move forward together. What unites us is a shared comprehensive approach to quality. The costs of quality are multifaceted: scrap, training, penalties, recalls, and more. Trigo now allows us to operate beyond Europe—in the United States, Canada, Brazil, India, and more recently South Korea—with an unmatched level of responsiveness.
What are the key trends in industrial quality control that Scortex anticipates?
Hugues Poiget: We aim to support quality controllers in all their key tasks: sparing them from eight-hour shifts of inspecting parts for anomalies, speeding up their ability to distinguish between acceptable and unacceptable anomalies, and providing quality data so they can quickly adjust sorting criteria based on production volumes. One major trend we anticipate is that AI-based tools will rapidly become commodities. The recent example of ChatGPT is a case in point. AI is entering everyday life and is already making its way into factories. This will, among other things, give manufacturers a competitive edge. Another trend is the need to reduce the environmental impact of industry. At Scortex, we understand the importance of reconciling production requirements with quality obligations. This is essential for maintaining a certain standard of living accessible to the majority. Tools like ours, by improving production line efficiency, help minimize the use of energy and raw materials.
Why do manufacturers choose Scortex for their automated quality control needs?
Hugues Poiget: At Scortex, we’re not afraid to roll up our sleeves. This is necessary to move from proof of concept to a system fully integrated into a production line. Our clients come to us looking for a powerful yet simple solution to the complex problem of visual inspection. Our Spark product combines a tool that can be used by a quality operator directly on the production line with a control tower, called the Quality Center, where quality data from the factory is aggregated to optimize production. Scortex provides everything—from hardware to software to algorithms. And because quality is constantly evolving, our teams are ready to support manufacturers at every stage of the project.
What a pleasure it is to hear one of our clients tell us they reduced their scrap rate from 7% to 2% in just one month!
Here are some other articles that might interest you:

Let's discuss your quality today.

Scortex team is happy to answer your questions.
Let's discuss your quality today.

Scortex team is happy to answer your questions.
Join our newsletter
Join our newsletter