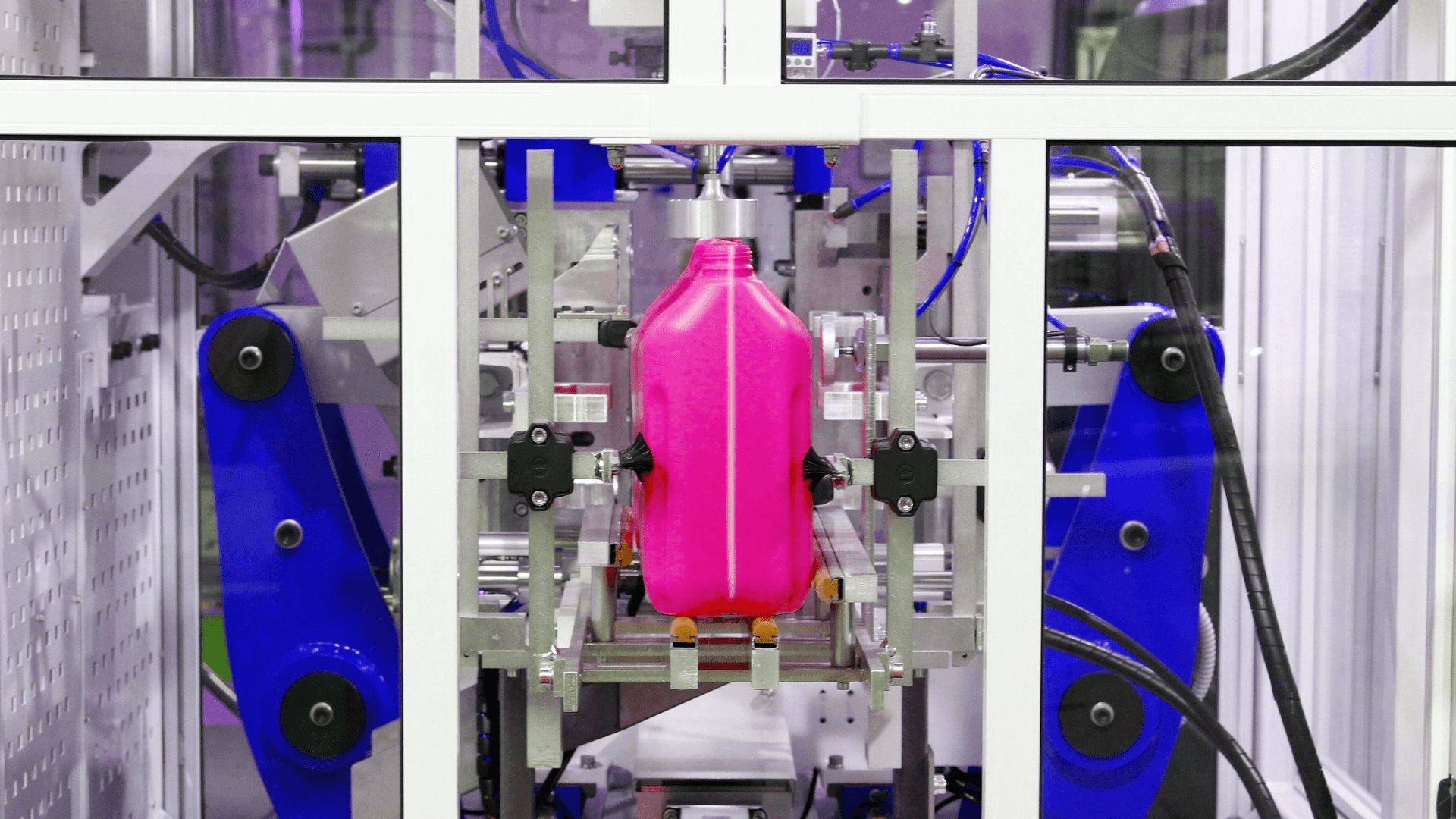
Injection molding: definition and process overview
Published on
Aug 28, 2024
by
Scortex team
Injection molding is a widely used manufacturing technique for producing plastic parts efficiently and cost-effectively. This method is essential across various industrial sectors, including automotive, electronics, packaging, and consumer goods. This article delves into the injection molding process, its advantages, applications, and the associated technologies that ensure high-quality production.
Definition of injection molding
Injection molding is a molding process that involves injecting molten plastic into a closed mold. Once cooled, the plastic hardens, taking the shape of the mold, resulting in a solid and precise part.
How injection molding works
Material preparation:
Plastic pellets, typically in the form of thermoplastic resin, are loaded into the injection molding machine's hopper. Common materials used include polypropylene (PP), polyethylene (PE), polystyrene (PS), and acrylonitrile butadiene styrene (ABS).Plastic melting:
The plastic pellets are heated in the machine's barrel until they melt. A reciprocating screw system transports and mixes the molten plastic to ensure a uniform consistency.Injection into the mold:
The molten plastic is injected at high pressure into a closed mold using a screw or piston. The mold, usually made of steel or aluminum, can be designed to produce simple or complex parts.Cooling:
After being injected into the mold, the plastic begins to solidify as it cools. The mold is often equipped with cooling channels to accelerate this process and ensure uniform solidification.Part ejection:
Once cooled, the mold opens, and the molded part is ejected using pins or ejector plates. The part may then undergo secondary processing to remove any excess material, known as flash.
Advantages of injection molding
Efficiency and speed:
Injection molding is a fast process capable of producing a large number of parts in a short time, making it a cost-effective method for mass production.Precision and repeatability:
Injection molding allows for the production of parts with tight tolerances and high precision, ensuring consistent dimensions and characteristics.Material flexibility:
A wide range of plastic materials can be used, allowing the selection of the most appropriate material based on required mechanical, thermal, and chemical properties.Complex shapes:
Injection molding enables the creation of complex and detailed shapes that would be challenging or impossible to achieve with other manufacturing methods.
Applications of injection molding
Automotive:
Automotive parts such as dashboards, bumpers, and engine components are often manufactured through injection molding due to their durability and lightweight properties.Electronics:
Enclosures for electronic devices, connectors, and insulating components are commonly produced by injection molding for their precision and ability to protect internal circuits.Packaging:
Containers, caps, and rigid plastic packaging are manufactured via injection molding for their cost-effectiveness and ability to securely preserve products.Consumer goods:
Toys, household items, and tools are frequently produced through injection molding for their robustness and appealing aesthetics.
Advanced technologies in injection molding
Gas-assisted injection molding:
This technology uses gas to create cavities within molded parts, reducing weight and enhancing structural strength.Multi-material injection molding:
This method allows multiple different materials to be injected into the same mold, producing parts with varied material properties in different sections.Microcellular injection molding:
This technique introduces microcells of air into the molten plastic, reducing the part's weight and improving its thermal and acoustic properties.Automated quality control:
Industrial vision systems and IoT sensors are used to monitor the injection molding process in real-time, detecting defects and ensuring the conformity of produced parts.
Practical applications and case studies
Medical industry:
Companies producing plastic syringes, for example, integrate industrial vision systems to inspect each part in real time. This reduces defect rates and ensures the safety of medical products.Consumer electronics:
Manufacturers of smartphones or OEM components for smartphones use microcellular injection molding to produce lighter and stronger casings while maintaining high dimensional accuracy.Packaging industry:
Packaging companies adopt gas-assisted injection molding technology to produce lighter bottle caps, reducing transport costs and carbon emissions.
Injection molding is a versatile and efficient manufacturing technique that offers numerous advantages in terms of precision, speed, and material flexibility. By leveraging advanced technologies and implementing rigorous quality controls, companies can enhance product quality and meet the growing market demands. Spark by Scortex, with its ability to automate and optimize production processes through artificial intelligence, represents an ideal solution for companies looking to maximize the benefits of injection molding while maintaining high-quality standards.
Other articles you might be interested in:
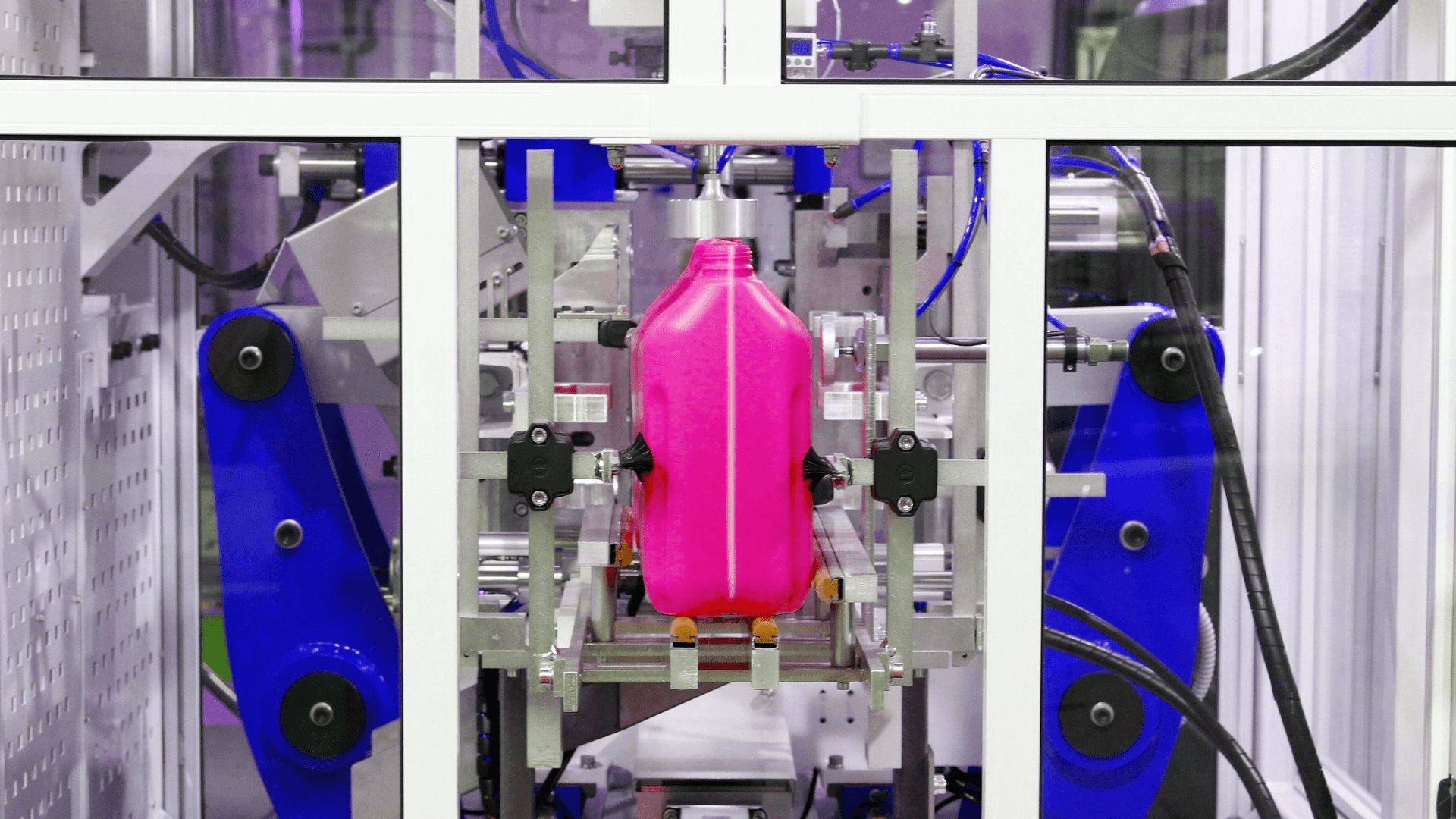
Injection molding: definition and process overview
Published on
Aug 28, 2024
by
Scortex team
Injection molding is a widely used manufacturing technique for producing plastic parts efficiently and cost-effectively. This method is essential across various industrial sectors, including automotive, electronics, packaging, and consumer goods. This article delves into the injection molding process, its advantages, applications, and the associated technologies that ensure high-quality production.
Definition of injection molding
Injection molding is a molding process that involves injecting molten plastic into a closed mold. Once cooled, the plastic hardens, taking the shape of the mold, resulting in a solid and precise part.
How injection molding works
Material preparation:
Plastic pellets, typically in the form of thermoplastic resin, are loaded into the injection molding machine's hopper. Common materials used include polypropylene (PP), polyethylene (PE), polystyrene (PS), and acrylonitrile butadiene styrene (ABS).Plastic melting:
The plastic pellets are heated in the machine's barrel until they melt. A reciprocating screw system transports and mixes the molten plastic to ensure a uniform consistency.Injection into the mold:
The molten plastic is injected at high pressure into a closed mold using a screw or piston. The mold, usually made of steel or aluminum, can be designed to produce simple or complex parts.Cooling:
After being injected into the mold, the plastic begins to solidify as it cools. The mold is often equipped with cooling channels to accelerate this process and ensure uniform solidification.Part ejection:
Once cooled, the mold opens, and the molded part is ejected using pins or ejector plates. The part may then undergo secondary processing to remove any excess material, known as flash.
Advantages of injection molding
Efficiency and speed:
Injection molding is a fast process capable of producing a large number of parts in a short time, making it a cost-effective method for mass production.Precision and repeatability:
Injection molding allows for the production of parts with tight tolerances and high precision, ensuring consistent dimensions and characteristics.Material flexibility:
A wide range of plastic materials can be used, allowing the selection of the most appropriate material based on required mechanical, thermal, and chemical properties.Complex shapes:
Injection molding enables the creation of complex and detailed shapes that would be challenging or impossible to achieve with other manufacturing methods.
Applications of injection molding
Automotive:
Automotive parts such as dashboards, bumpers, and engine components are often manufactured through injection molding due to their durability and lightweight properties.Electronics:
Enclosures for electronic devices, connectors, and insulating components are commonly produced by injection molding for their precision and ability to protect internal circuits.Packaging:
Containers, caps, and rigid plastic packaging are manufactured via injection molding for their cost-effectiveness and ability to securely preserve products.Consumer goods:
Toys, household items, and tools are frequently produced through injection molding for their robustness and appealing aesthetics.
Advanced technologies in injection molding
Gas-assisted injection molding:
This technology uses gas to create cavities within molded parts, reducing weight and enhancing structural strength.Multi-material injection molding:
This method allows multiple different materials to be injected into the same mold, producing parts with varied material properties in different sections.Microcellular injection molding:
This technique introduces microcells of air into the molten plastic, reducing the part's weight and improving its thermal and acoustic properties.Automated quality control:
Industrial vision systems and IoT sensors are used to monitor the injection molding process in real-time, detecting defects and ensuring the conformity of produced parts.
Practical applications and case studies
Medical industry:
Companies producing plastic syringes, for example, integrate industrial vision systems to inspect each part in real time. This reduces defect rates and ensures the safety of medical products.Consumer electronics:
Manufacturers of smartphones or OEM components for smartphones use microcellular injection molding to produce lighter and stronger casings while maintaining high dimensional accuracy.Packaging industry:
Packaging companies adopt gas-assisted injection molding technology to produce lighter bottle caps, reducing transport costs and carbon emissions.
Injection molding is a versatile and efficient manufacturing technique that offers numerous advantages in terms of precision, speed, and material flexibility. By leveraging advanced technologies and implementing rigorous quality controls, companies can enhance product quality and meet the growing market demands. Spark by Scortex, with its ability to automate and optimize production processes through artificial intelligence, represents an ideal solution for companies looking to maximize the benefits of injection molding while maintaining high-quality standards.
Other articles you might be interested in:

Let's discuss your quality today.

Scortex team is happy to answer your questions.
Let's discuss your quality today.

Scortex team is happy to answer your questions.
Join our newsletter
Join our newsletter