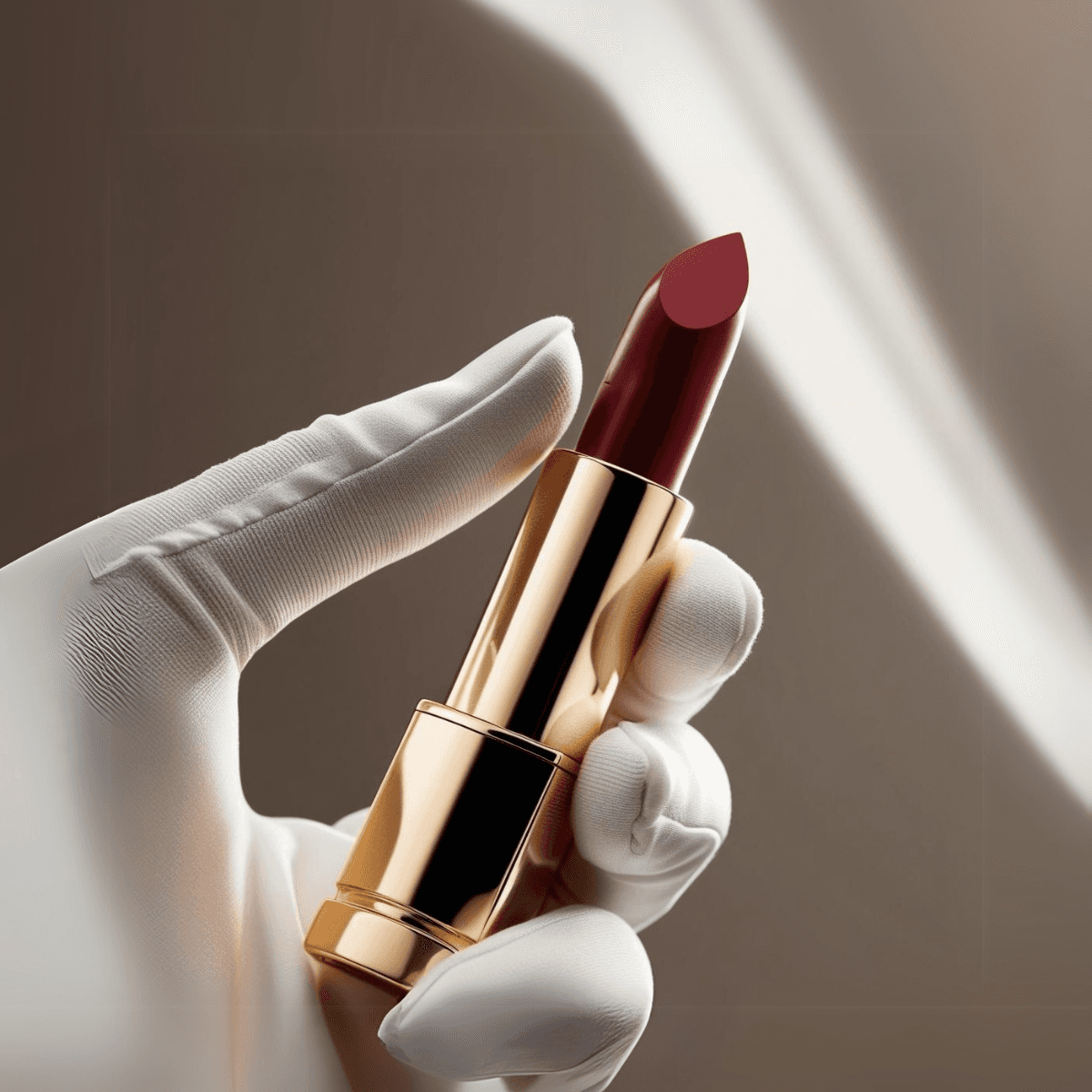
From visual fatigue to visual excellence: how a leading luxury cosmetics brand revolutionized their lipstick quality control
Published on
Nov 12, 2024
by
L'équipe Scortex
Every lipstick tells a story of beauty. But for Marie, Head of Quality at one of Europe's most prestigious cosmetics brands, each lipstick also told a story of mounting pressure. 'With hundreds of shades, constant new launches, and luxury consumers expecting perfection, our quality control teams were fighting an uphill battle,' she recalls.
Standing in her factory in early 2023, Marie watched her quality control operators meticulously inspecting thousands of lipsticks. Despite their expertise, she knew they were facing an impossible task. Operator fatigue was leading to inconsistent results - some flawed products reached customers, while perfectly good lipsticks were being discarded. With the beauty industry's rapid innovation cycles demanding ever more frequent product launches, the traditional manual inspection system was reaching its breaking point.
'We were losing talented operators to burnout, and our waste rates were affecting both our sustainability goals and our bottom line,' Marie explains. 'When you're handling premium products at our scale - across multiple production lines in Europe and the USA - even a 1% error rate translates to significant losses.'
The challenge was complex:
Modern production lines sat alongside equipment dating back decades
Each new product launch brought unique quality control challenges
Premium market positioning demanded zero tolerance for defects
Labor shortages made recruiting quality control operators increasingly difficult
Visual fatigue led to inconsistent inspection results
Previous attempts to automate quality control had fallen short. 'We tested numerous inspection systems,' Marie shares, 'but none could match the discerning eye of our experienced operators - until now.'
The beauty industry's struggle with automated quality control runs deeper than most realize. 'Vision systems have long been the gold standard in many manufacturing sectors,' explains Marie, 'but luxury cosmetics present unique challenges that have stumped even the most advanced systems.'
Traditional vision systems face multiple obstacles in lipstick inspection:
Highly reflective surfaces that create unpredictable light patterns
Subtle color variations that can mask real defects
Complex geometrical shapes requiring multiple-angle inspection
Hundreds of different shades and finishes to master
New formulations constantly pushing the boundaries of traditional inspection methods
'What is it about their algorithm that makes it better, while it is known that it is a notoriously difficult use case in the vision industry?' Marie's question cuts to the heart of a challenge that has frustrated quality managers across the cosmetics industry for years. Previous attempts at automation typically failed in one of three ways:
False positives that led to excessive waste
Missed defects due to complex surface properties
Inability to adapt to new product variations
Industry statistics painted a stark picture:
75% of vision system implementations in cosmetics quality control failed to meet expectations
Traditional systems required up to 3 months of recalibration for each new product launch. Even AI based system for defect detection were too slow to adapt due to extra reliance on internal or external AI engineer for the program creation.
Most factories resigned themselves to manual inspection as the "necessary evil" of luxury cosmetics production
This context makes the transformation even more remarkable. As one Quality Control Supervisor observed: 'The first 30 minutes of inspection, performance was quite the same between human and Scortex. After 30 minutes, the human attention was already decreasing while Scortex was constant. Scrap rate is the same, but if it was human only, the missed defects would have been higher.'
This breakthrough challenged long-held industry assumptions about automated inspection capabilities. While other sectors like automotive or electronics had successfully automated their quality control years ago, luxury cosmetics remained a final frontier - until now.
The Path to transformation
After extensive research, Marie and her team partnered with us to implement an AI-powered quality control system that could match - and ultimately exceed - human inspection capabilities. What set this solution apart was particularly striking to the Quality Team Lead: 'What is it about their algorithm that makes it better, while it is known that it is a notoriously difficult use case in the vision industry?'
The implementation revealed a compelling answer through direct performance comparisons. As one Quality Control Supervisor observed: 'The first 30 minutes of inspection, performance was quite the same between human and Scortex. After 30 minutes, the human attention was already decreasing while Scortex was constant. Scrap rate is the same, but if it was human only, the missed defects would have been higher.'
Key transformation milestones:
Maintained consistent defect detection rate across entire shifts
Eliminated the variable of operator fatigue in quality control
Achieved uniform inspection quality regardless of shift length or time of day
The results: beyond quality control
Within six months, the transformation exceeded even the most optimistic expectations:
Quality impact:
Defect detection rate improved to a point where no critical defects are delivered
False rejection rate reduced, keeping the scrap level steady despite increased ejection of critical defects, saving premium products from unnecessary waste
Consistency in quality control maintained even during 8-hour shifts
Human impact:
'Our quality control team's role has evolved from repetitive inspection to high-value quality management,' beams Marie. 'Instead of suffering from visual fatigue, our operators now focus on continuous improvement and innovation.'
Business impact:
Operational costs reduced through automation of manual tasks, decreased waste and improved efficiency. Up to 2 operators per shift were removed from the inspection task.
Production capacity increased by 25% due to faster, more reliable inspection
New product launch time reduced thanks to rapid inspection program creation: only 15 minutes to create a new inspection program
‘The power of these results lies in their consistency. While the initial scrap rates remained similar to human inspection, the system's unwavering attention meant that fewer defective products reached customers - a critical factor for a luxury brand where each product represents not just a sale, but the brand's reputation’
Future vision
Building on this success, Marie and her team are now exploring additional applications of the technology. 'This journey has shown us that when you combine human expertise with the right technology, you don't just solve problems - you create new possibilities,' she concludes.
Scortex system will be deployed on more than 10 lines in the customer’s factories.
Here are some other articles that might interest you:
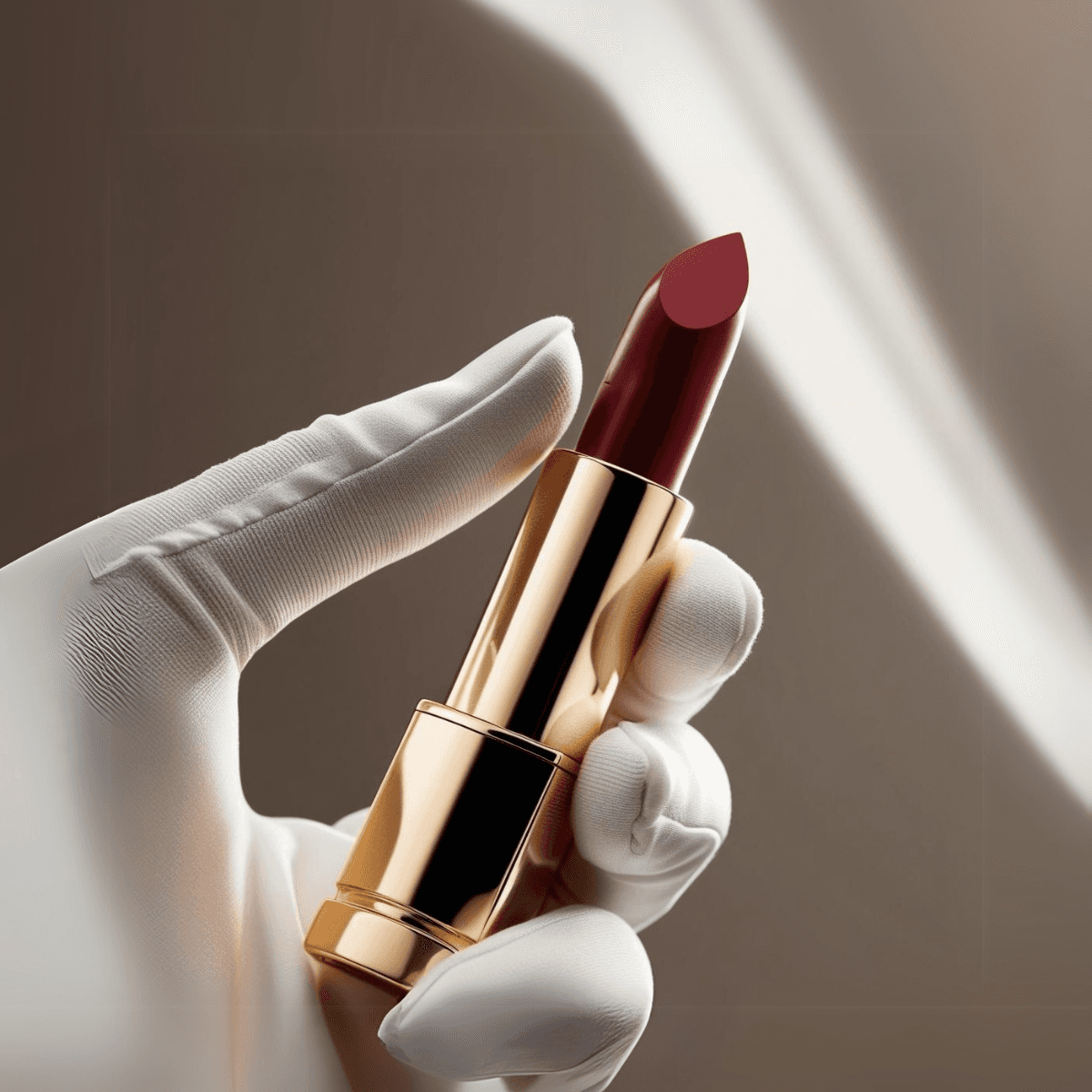
From visual fatigue to visual excellence: how a leading luxury cosmetics brand revolutionized their lipstick quality control
Published on
Nov 12, 2024
by
L'équipe Scortex
Every lipstick tells a story of beauty. But for Marie, Head of Quality at one of Europe's most prestigious cosmetics brands, each lipstick also told a story of mounting pressure. 'With hundreds of shades, constant new launches, and luxury consumers expecting perfection, our quality control teams were fighting an uphill battle,' she recalls.
Standing in her factory in early 2023, Marie watched her quality control operators meticulously inspecting thousands of lipsticks. Despite their expertise, she knew they were facing an impossible task. Operator fatigue was leading to inconsistent results - some flawed products reached customers, while perfectly good lipsticks were being discarded. With the beauty industry's rapid innovation cycles demanding ever more frequent product launches, the traditional manual inspection system was reaching its breaking point.
'We were losing talented operators to burnout, and our waste rates were affecting both our sustainability goals and our bottom line,' Marie explains. 'When you're handling premium products at our scale - across multiple production lines in Europe and the USA - even a 1% error rate translates to significant losses.'
The challenge was complex:
Modern production lines sat alongside equipment dating back decades
Each new product launch brought unique quality control challenges
Premium market positioning demanded zero tolerance for defects
Labor shortages made recruiting quality control operators increasingly difficult
Visual fatigue led to inconsistent inspection results
Previous attempts to automate quality control had fallen short. 'We tested numerous inspection systems,' Marie shares, 'but none could match the discerning eye of our experienced operators - until now.'
The beauty industry's struggle with automated quality control runs deeper than most realize. 'Vision systems have long been the gold standard in many manufacturing sectors,' explains Marie, 'but luxury cosmetics present unique challenges that have stumped even the most advanced systems.'
Traditional vision systems face multiple obstacles in lipstick inspection:
Highly reflective surfaces that create unpredictable light patterns
Subtle color variations that can mask real defects
Complex geometrical shapes requiring multiple-angle inspection
Hundreds of different shades and finishes to master
New formulations constantly pushing the boundaries of traditional inspection methods
'What is it about their algorithm that makes it better, while it is known that it is a notoriously difficult use case in the vision industry?' Marie's question cuts to the heart of a challenge that has frustrated quality managers across the cosmetics industry for years. Previous attempts at automation typically failed in one of three ways:
False positives that led to excessive waste
Missed defects due to complex surface properties
Inability to adapt to new product variations
Industry statistics painted a stark picture:
75% of vision system implementations in cosmetics quality control failed to meet expectations
Traditional systems required up to 3 months of recalibration for each new product launch. Even AI based system for defect detection were too slow to adapt due to extra reliance on internal or external AI engineer for the program creation.
Most factories resigned themselves to manual inspection as the "necessary evil" of luxury cosmetics production
This context makes the transformation even more remarkable. As one Quality Control Supervisor observed: 'The first 30 minutes of inspection, performance was quite the same between human and Scortex. After 30 minutes, the human attention was already decreasing while Scortex was constant. Scrap rate is the same, but if it was human only, the missed defects would have been higher.'
This breakthrough challenged long-held industry assumptions about automated inspection capabilities. While other sectors like automotive or electronics had successfully automated their quality control years ago, luxury cosmetics remained a final frontier - until now.
The Path to transformation
After extensive research, Marie and her team partnered with us to implement an AI-powered quality control system that could match - and ultimately exceed - human inspection capabilities. What set this solution apart was particularly striking to the Quality Team Lead: 'What is it about their algorithm that makes it better, while it is known that it is a notoriously difficult use case in the vision industry?'
The implementation revealed a compelling answer through direct performance comparisons. As one Quality Control Supervisor observed: 'The first 30 minutes of inspection, performance was quite the same between human and Scortex. After 30 minutes, the human attention was already decreasing while Scortex was constant. Scrap rate is the same, but if it was human only, the missed defects would have been higher.'
Key transformation milestones:
Maintained consistent defect detection rate across entire shifts
Eliminated the variable of operator fatigue in quality control
Achieved uniform inspection quality regardless of shift length or time of day
The results: beyond quality control
Within six months, the transformation exceeded even the most optimistic expectations:
Quality impact:
Defect detection rate improved to a point where no critical defects are delivered
False rejection rate reduced, keeping the scrap level steady despite increased ejection of critical defects, saving premium products from unnecessary waste
Consistency in quality control maintained even during 8-hour shifts
Human impact:
'Our quality control team's role has evolved from repetitive inspection to high-value quality management,' beams Marie. 'Instead of suffering from visual fatigue, our operators now focus on continuous improvement and innovation.'
Business impact:
Operational costs reduced through automation of manual tasks, decreased waste and improved efficiency. Up to 2 operators per shift were removed from the inspection task.
Production capacity increased by 25% due to faster, more reliable inspection
New product launch time reduced thanks to rapid inspection program creation: only 15 minutes to create a new inspection program
‘The power of these results lies in their consistency. While the initial scrap rates remained similar to human inspection, the system's unwavering attention meant that fewer defective products reached customers - a critical factor for a luxury brand where each product represents not just a sale, but the brand's reputation’
Future vision
Building on this success, Marie and her team are now exploring additional applications of the technology. 'This journey has shown us that when you combine human expertise with the right technology, you don't just solve problems - you create new possibilities,' she concludes.
Scortex system will be deployed on more than 10 lines in the customer’s factories.
Here are some other articles that might interest you:

Let's discuss your quality today.

Scortex team is happy to answer your questions.
Let's discuss your quality today.

Scortex team is happy to answer your questions.
Join our newsletter
Join our newsletter